

I am sure I’m missing something due to my lack of ISO education, but pylfrm’s example (and also OP original example) looks pretty basic. Why straightness tolerance does not matter in ISO? (I am sure matter in ASME as a derived median line straightness, but that is beside of the point) Sorry to be nosy, but could you, please explain a bit more?
#ISO 2768 MK ERKLÄRUNG PLUS#
If you want to accept all good parts, the straightness tolerance must be allowed for and the ring gage hole diameter should be 9.5 (with a plus tolerance). If you want to reject all bad parts, the straightness tolerance doesn't matter and the ring gage hole diameter should be 8.5 (with a minus tolerance).
#ISO 2768 MK ERKLÄRUNG PDF#
Imagine you have an external cylindrical surface with a diameter tolerance of 8 +/- 0.5 and a straightness tolerance of 1.0 MMC, and you want a GO ring gage to check compliance with the upper limit of the diameter tolerance. Acces PDF General Tolerances Iso 2768 Mk Sdocuments Com of the most common dimensioning and tolerancing specifications.The book may be used for engineering courses and for professional grade programmes, and it has been designed to cover the fundamental geometric tolerancing applications as well as the more advanced ones. I realize you are talking about the nominal gage dimension. RE: ISO 2768-mK and gage size SeasonLee (Mechanical) 29 Apr 19 19:08 If you want to be able to gauge this cylinder it would be advisable to invoke the Envelope principle for this feature.
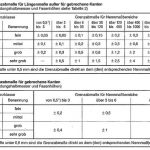
If the diameter dimension has, additionally to the size tolerance, an encircled "E" behind it then you treat it like an envelope (just as with ASME 14.5) The straightness allowance would however depend on the length of that cylinder. The resulting cylinder would still be allowed to have local diameters between 11.9 mm and 12.2 mm. Given in Table 4 the value of 0,2 mm, therefore, Of 0,4 mm which is greater than the value of 0,2 mm These deviations lead to the numerical value The permissibleĭeviations for the diameter of 25 mm are ± 0,2 mm. The general tolerances in accordance with the Tolerance on circularity is equal to the numerical

Indicated directly on the drawing the general The permissible deviation of the diameter is

Outside Diameter:15.9mm Inside Diameter: 6.4mm Thickness: 3. So the diameter of each ring can be anywhere between 11.9 mm and 12.2 mm but its circularity has to be within a 0.2 mm boundary. Hello All, I am trying to understand which table I need to look at for ISO 2768-mK based on the tolerance example for a Flat washer I was given below. In your case - linear diameter tolerance is larger (+0.2/-0.1 = 0.3) than the allowable circularity deviation (0.2) - the circularity deviation of every ring along that cylinder is not allowed to exceed 0.2, regardless of the diameter size. ISO 2768-K would limit the total permissible circularity deviation to 0.2 mm even if the permissible linear diameter deviation is greater. However, if as you indicate, the 12 mm diameter has an individual tolerance assigned (+0.2/-0.1) then the first part of ISO 2768 (the "m") does not cover this dimension.īut without additional geometric tolerances the "K" would still define the maximum allowable circularity and straightness deviations. Geometrical tolerances may be used even if theįeatures are everywhere at their maximum material (see ISO 8015), general geometrical tolerancesĪpply independently of the actual local size of the ISO 2768 is mainly for parts that are manufactured by way of machining or removal of materials.According to the principle of independency ISO 2768 and derivative geometrical tolerance standards are intendedto simplify drawing specifications for mechanical tolerances. Variations on dimensions without tolerance values are according to " ISO 2768".
